Like many industrial facilities across the country, your plant has probably started converting their legacy lighting system over to LED lighting. However, with hundreds of fixture manufacturers now on the market, unless you have an engineering or maintenance department with a bunch of spare time, choosing the right fixture for the various applications in your facility can be both complex and time-consuming.
This often leads to oversimplifying the procurement process and basing the purchasing decision on first cost alone. This mistake, which essentially assumes all LED fixtures are created equal, can literally cost your company hundreds of thousands of dollars without you even knowing it.
To help your company avoid this trap, in this post we’ll break down some of the industry’s best practices on selecting fixtures and designing lighting upgrades for specific applications by looking at things like fixture specifications, life cycle cost analysis and photometrics (the layout of the fixtures).
By taking these three categories into account, you can actually give your company an energy advantage over your competition and save scarce capital and resources for your core business.
LED Fixture Specifications
The first step in selecting a LED fixture is determining the type of fixture you need, along with any desired features and qualifications. While the below list is by no means meant to be comprehensive, which would take way more time than we have here, it should give you a feel for the items that would be good to consider in the selection process.
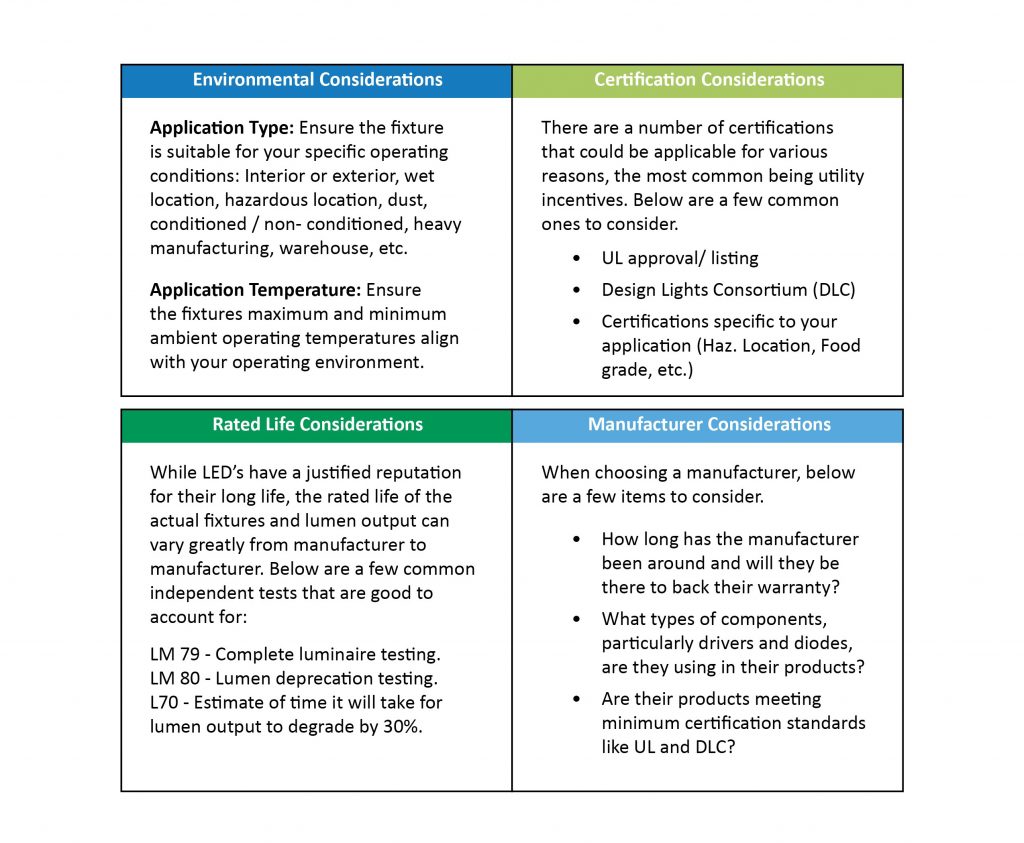
Once you’ve determined an acceptable specification for your fixture, it’s time to compare your options.
LED First Cost vs Cost of Ownership (The Life Cycle Cost)
Like many equipment purchases, the first cost of a LED lighting fixture (the cost to purchase the material itself) is actually just the beginning of your investment. The real cost of the fixture is the energy cost to operate the fixture, the cost of ownership. In general, 10% – 30% of the fixture’s life cycle cost is the first cost and 70% – 90% of the cost is the energy used to operate it. So when choosing a fixture for a given application, wouldn’t it be wise to emphasize the evaluation of the cost to operate your chosen fixture? As you’ll see below, even LED fixtures can vary greatly in operational costs from manufacturer to manufacturer.
Comparing Life-Cycle Costs Between Fixtures
To illustrate this point, let’s take a look at three different LED high bay fixtures from various manufacturers labeled: Manufacturer 1, Manufacturer 2 and Manufacturer 3. By looking at the chart below, it’s clear that most procurement teams would purchase manufacturer #1, the low-cost provider, when in reality this would end up costing their facility $60,000 – $90,000 more than the higher first cost alternatives. This is without taking into account any of the other criteria we’ll review.
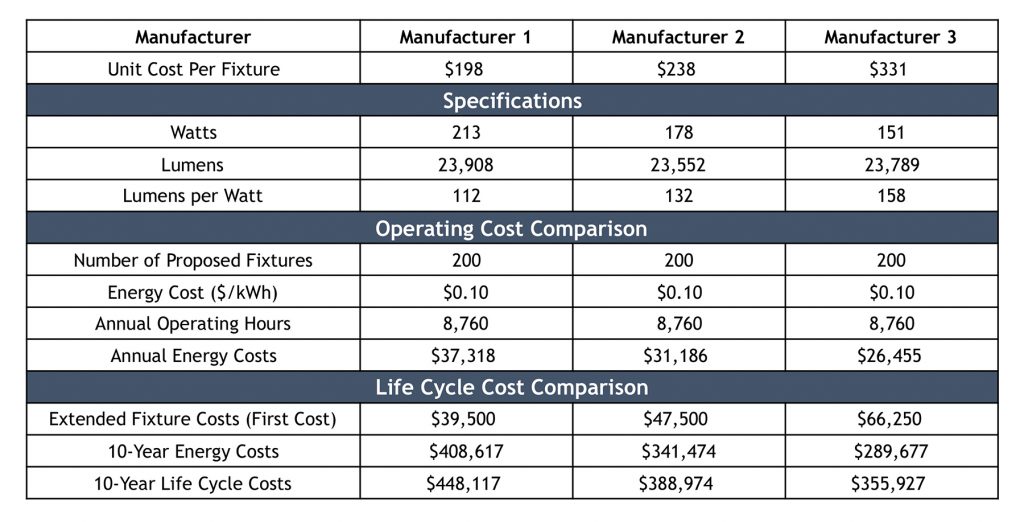
Lighting Photometrics and Layout Design
Just as it costs less energy to operate certain fixtures, it turns out, it can also require fewer fixtures to light a given space when compared to others. It’s also critical to realize that replacing your fixtures one for one is not always the best design option. Having proper photometrics developed for your application can be key and will allow you to:
- Minimize the number of fixtures used to light a given space.
- Ensure the space is evenly lit, a term called lighting uniformity, with a max to min ratio appropriate for the given application.
As an example, let’s compare two layout designs for a manufacturing facility. The first layout is for the existing system lighting the plant, which has (285) 340 watt 6 Lamp T5 High Bays and is achieving approximately 75 foot candles.
The second layout is the proposed LED design that only uses (185) 151 watt LED high Bays achieving the same foot candle level.
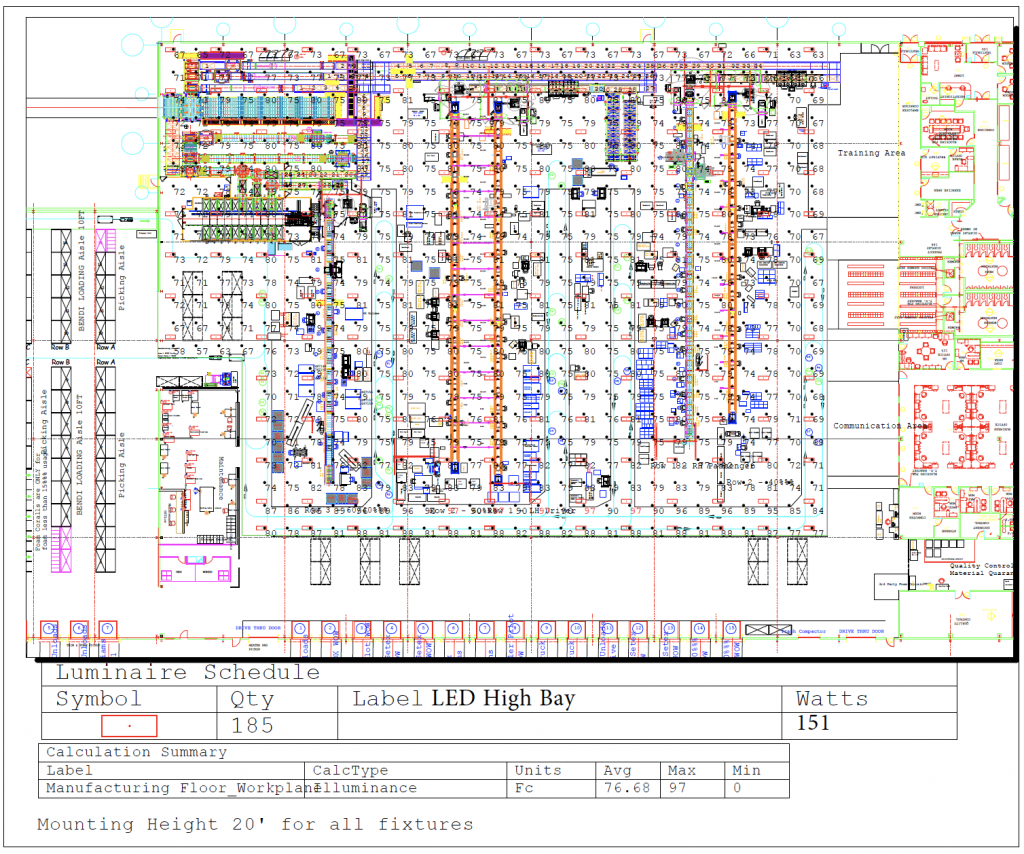
By optimizing the fixture spacing and redesigning the existing lighting system, we were able to eliminate 100 fixtures and substantially reduce material, labor and ongoing energy costs for the system as a whole.
Conclusions
As you can see, if you want to avoid costly mistakes in upgrading your company’s lighting system, it’s critical to put in the work and do the research to design the system properly. Or hire an experienced company like SEMCO to design it for you. The initial energy assessment is free, and on average, 20% – 40% of our project’s costs are covered with little known incentives.
To learn more, contact us to schedule a time to discuss any of your energy efficiency needs.