A 2019 Ferrari 488 Spider is a manufacturing feat of beauty. Every time I see one I’m left in awe of its sleek design, beautiful aesthetics and performance capabilities that are next to none. And yet, I also feel a small sense of disappointment in that most of us will never be able to afford one because, for a 2019 model, you’re looking at a base price of a cool $288,000.
What most plant managers and operators don’t realize though, is that their plant is effectively paying for this type of asset, or close to it, every year, year over year, through the operation of their compressed air system.
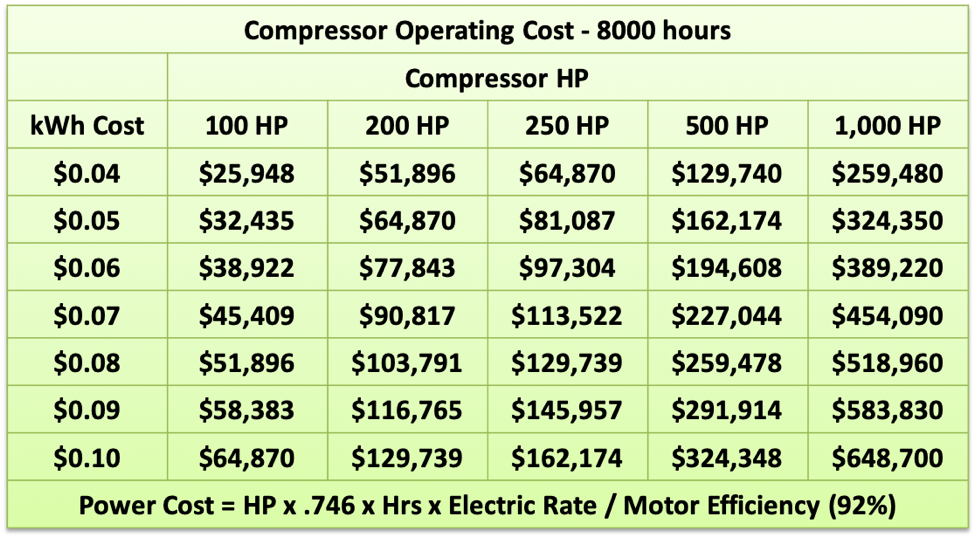
That’s right, compressed air is probably one of your most inefficient and expensive assets to operate, requiring seven units of energy input for just one unit of energy output. Because of this, it’s critical to not only measure your compressed air systems operation but take steps to manage and track its usage as efficiently as possible. Unfortunately, this is a feat very few manufacturers have the time, knowledge or resources to accomplish.
At SEMCO, it’s our mission to shine a spotlight on energy in-efficiency and provide manufacturers with the turnkey solutions and tools they need to help manage and control their energy costs.
Specifically, with compressed air, there are three areas of the system we will help you control to reduce your operating costs by an average of 35% – 50%. These three areas include:
- Artificial Demand & Site Pressure Issues
- Inappropriate Uses
- System Leaks.
All of these coincide with one another and result in a substantial opportunity for savings.
Eliminating Artificial Demand & Site Pressure Problems
Going back to our Ferrari example, imagine driving the beautiful asset your paying for every year down the high-way, cruising at 80 MPH (because you don’t want to get a ticket) and all of the sudden a small parachute drops out of the back and slows you down.
Now you don’t know the problem is a small parachute, you can’t see it and it could be anything, but what you do know is that you have to get to where you’re going in the amount of time you’ve allotted, so instead of stopping to assess and address the problem, what do you do? Just give it a little more gas!
We see this scenario play out over and over again within plants. Compressed air system issues occur, the maintenance staff does not have the knowledge, tools or resources to diagnose and fix the problems, so instead they are forced to crank up the system pressure and continue business as usual. This scenario can repeat its self over a number of years and before you know it, you have a system that only needs to run at 80PSI, operating at 120PSI.
This is a very costly mistake as every 2 PSI increase in system pressure equals a 1% increase in overall energy usage for the system. The higher pressure further causes unregulated end uses in the plant to consume more compressed air, increasing energy costs an approximate additional 10%.
“Every 2 PSI increase in system pressure equals a 1% increase in overall energy usage.”
Our engineering team specializes in identifying what your optimal site pressure needs to be by evaluating the system as a whole and engineering strategic solutions to lower header pressure to an optimal level, eliminating artificial demand. Common examples of this include:
- Installing ample compressed air storage to improve the speed and torque of a given application, protect critical applications from pressure fluctuations, support events in the system within an allowable pressure drop, and more. Most plants have only a fraction of the storage they need.
- Eliminating pressure problems that increase demand. Examples of this will vary greatly by plant and industry but in our experience, 20% – 30% of the horsepower on line in most systems is due to unnecessary high system pressure.
- Identifying, tagging and fixing compressed air leaks. This should and will always be an ongoing maintenance task.
These examples segue into the next two items we typically evaluate within a system.
Eliminating Inappropriate Uses
Most manufacturers drive their Ferraris without keeping track of how much gas they’re putting in the tank, or more specifically, how much electricity it costs to operate the compressed air system.
Without this critical key Performance Indicator (KPI), it’s easy for site personal to use the compressors for any application they see fit, including applications that could be better and more cost effectively served by an alternative solution. There are many possible examples of inappropriate uses but a few include:
- Using compressed air to blow off and clean equipment throughout the plant during production and non-production hours.
- Using compressed air to keep production photo eyes or specific manufacturing process clear of debris.
- Using pneumatic systems in the manufacturing process that can be better served by another solution.
Inappropriate uses of compressed air will vary widely by industry and are not always easy to identify. Utilizing an engineering team that has worked on many different types of systems in various applications is key.
Compressed Air Leaks
Compressed air leaks are a widely known opportunity by many plant operators, however it’s one that still often goes untouched. The real issue here is that operators do not have:
- An active way to identify, quantify and value the costs associated with system leaks.
- A way to measure, verify and report the successful repair of a given leak to management.
As the age old saying goes, if you can’t measure it, you can’t manage it, and compressed air systems are no exception.
By working with SEMCO, we will not only provide you with a turnkey solution to reduce energy costs, but we will also provide you with the tools that will enable your team to actively measure and monitor your systems over all energy usage.
Specific KPI’s will be determined to help your team recognize when there is an issue, or even receive notifications of such anywhere in the world.
Conclusions
Like many complex systems, there is no one size fits all solution for addressing compressor energy costs. Each facility and system will require its own unique mix of solutions to cost effectively eliminate energy waste and maintenance issues.
The real value SEMCO brings to the table is an experienced engineering team that can not only identify low ROI energy efficiency opportunities, but also supply your company with little known grants, rebates, tax incentives and low interest capital to help fund your projects.
Contact us here for your free energy assessment and learn how to start saving today!